The Role of EchoStat in Battery Cell Inspection
QA/QC in battery cell manufacturing is growing in importance as manufacturers try to compete on quality while lowering costs. Our EchoStat platform is a first-of-its-kind, non-invasive, fully automated, in-line battery cell inspection solution. With this blog post, we’re taking the opportunity to break down how EchoStat works and the role that ultrasound technology plays in the battery cell inspection process. We’ll break down the technical aspects of our product’s functionality and how they enable EchoStat to provide accurate detection of battery cell health.
Revolutionizing Battery Cell Inspection with Ultrasound and Machine Learning
By combining ultrasound technology with machine learning analytics, our cell inspection and analytics solutions offer reliable quality insights and high throughput capabilities, empowering manufacturers with rich, real-time data on cell health, performance and production line efficacy. EchoStat integrates seamlessly into the production line at multiple insertion points and inspects cells in seconds, rather than the weeks or even months that other methods can take, removing bottlenecks and empowering a more efficient production process.
Supplementation, Not Replacement
When it comes to QA/QC, accurate and efficient cell inspection will be critical for the manufacturing industry to meet soaring demand. As we’ve discussed in a previous post, there are major challenges with current testing methods. Fast inspection techniques often miss critical issues to prioritize speed. Comprehensive inspections are rarely fast and can only be applied to a small sample of randomly selected cells. Each leaves room for quality escapes, which can result in poor performance and field failures at best, or, at worst, safety events and vehicle recalls. Finally, many current inspection methods are destructive by nature—they require pushing the cells to failure or physically deconstructing them in order to get a closer look. This process is not only time-intensive, it also contributes to large amounts of scrap and higher production costs.
Integrating EchoStat into the battery production line equips manufacturers with the capability to comprehensively monitor the health of 100% of cells in production, all while avoiding previously known bottlenecks. EchoStat is engineered to redefine inspection standards, transcending the capabilities of existing inspection technologies( (such as optical inspection, electrical tests, X-rays, and CTs) rather than just complementing them. We emerge as a sophisticated alternative, driving the industry forward with enhanced insights and precision, thus asserting our competitive placement in the inspection technology landscape. By employing EchoStat at multiple stages of the production line—mainly focusing on the stages that follow electrode manufacturing—manufacturers can glean unparalleled intelligence and insights, diving deeper than ever before into cell quality and performance. This equips cell producers with actionable data, enabling more precise quality control and rapid, informed decision-making that legacy technologies alone may not fully support.
How EchoStat Works
Our EchoStat platform revolutionizes battery cell inspection through its two complementary components: ARRAY, our production-line product, and RASTER, our high-resolution product.
EchoStat ARRAY serves as the front-line guardian of cell quality, performing rapid, six-second inspections for 100% of cells on the production line. Compatible with any flat cell format (pouch or prismatic) and adaptable to various cell chemistries (e.g. LIB, Li-metal, Na+ ion, etc.), ARRAY is fully automated and seamlessly integrates into existing production lines at multiple insertion points, where fast quality checks are critical.
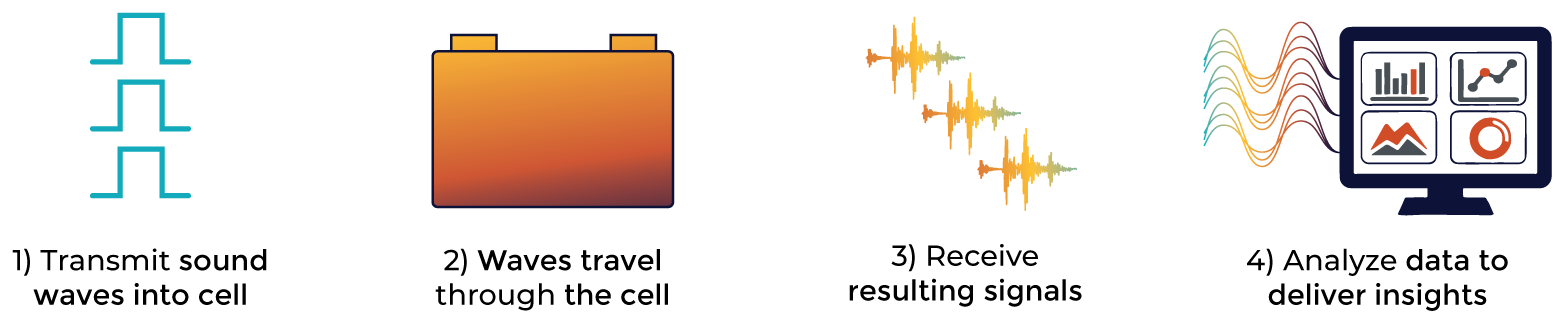
Here’s how it works: Multiple ultrasound transducer pairs are strategically positioned in a matrix across the entire face of the cells being tested. These transducers transmit precise sound waves, which interact with the internal materials of the cell. The resulting signals are received by transducers on the other side of the cell and provide vital information about its physical characteristics. This information correlates to the physical properties of the materials along with the health of the battery and helps us identify many potential issues. We take the raw acoustic data, extract meaningful information and process it using our advanced physics-based machine learning analytics to deliver actionable insights in real-time.
These insights include:
- Detection of potential production defects
- Prediction of battery life performance with over 85% accuracy
- Evaluation of electrolyte saturation quality
- Analysis on cell uniformity
In the unique application of identifying production defects, if ARRAY detects a potential issue, indicating a cell might not align with quality standard, that cell is automatically rerouted to EchoStat RASTER for an in-depth, high-resolution analysis specializing solely in defect detection.
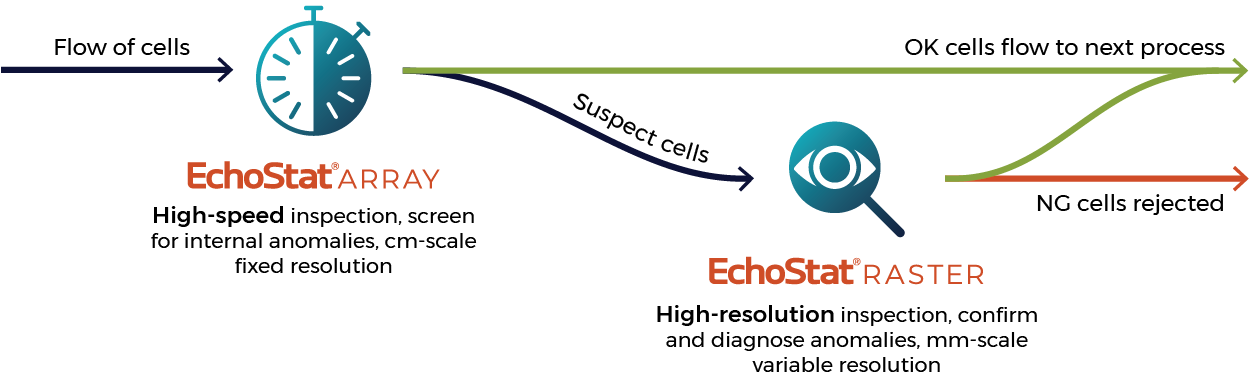
RASTER utilizes the same core ultrasound technology and machine learning models as ARRAY, but is designed to delve deeper into the detected anomalies. Depending on the customer’s specific requirements, this can be a comprehensive scan of up to 30 minutes for a thorough analysis, or a two-minute scan focusing on a particular aspect such as electrode misalignment. Because only a small fraction of cells flagged by ARRAY are sent to RASTER (for example, 3% of cells are flagged as possibly containing a defect), this detailed analysis can afford to be more time-intensive in order to focus on higher resolution while still scanning all of the cells. RASTER is also versatile – it can operate as an automated at-line system for cells flagged by ARRAY or as a standalone tool for deeper analytics, depending on a manufacturer’s unique needs and quality control strategy.
Together, ARRAY and RASTER form the complete EchoStat cell inspection solution, designed to empower manufacturers to scale production efficiently while maintaining the utmost quality and safety standards. By leveraging the unique properties of ultrasound waves—which vary based on the materials they pass through—and sophisticated physics-based machine learning models, our EchoStat inspection platform transforms acoustic data into actionable insights, allowing for informed, rapid decision-making and unrivaled control over cell quality.
Benefits of EchoStat in Battery Cell Inspection
Faster and More Accurate Detection
During various in-factory trials on commercial cells, EchoStat’s performance prediction models have predicted cell performance with accuracy ranging from 83% to 98%, and our anomaly detection models have identified cells containing separator defects with greater than 90% accuracy.
EchoStat is also able to detect errors closer in the process to where they actually occur, instead of the lag time of days or weeks experienced with end-of-line electrical inspection methods. This shortened feedback loop enables battery cell manufacturers to increase efficiency and yield. Additionally, our technology is able to aggregate data across the production line, from cell finishing to end-of-line QA/QC, providing greater insights to improve the overall process of quality monitoring and control.
EchoStat Production Line Insertion Points & Benefits
As we discussed in a previous blog post, there is a great need for non-destructive evaluation (NDE) methods like EchoStat’s ultrasonic inspection. We recommend reading that post for more information on the current best practices, challenges, and opportunities of NDE. Here will briefly outline the role that EchoStat will serve as an NDE method, as it integrates into multiple insertion points throughout the production process.
Electrolyte Fill and Soak
EchoStat quickly and accurately estimates electrolyte saturation quality without causing any damage to the cell. Ultrasound waves penetrate cell materials and their interactions with the electrolyte provide crucial data on saturation levels, critical to prevent lithium plating and internal shorts. EchoStat’s Electrolyte Saturation Quality model utilizes machine learning to analyze this data, enabling engineers to optimize fill rates and soak times to the second, and thereby minimizing manufacturing waste while ensuring cells have homogenous and complete electrolyte distribution before formation. This negates risks of dry spots, which can lead to local overheating and premature cell failure, offering a powerful means to preemptively troubleshoot this common problem.
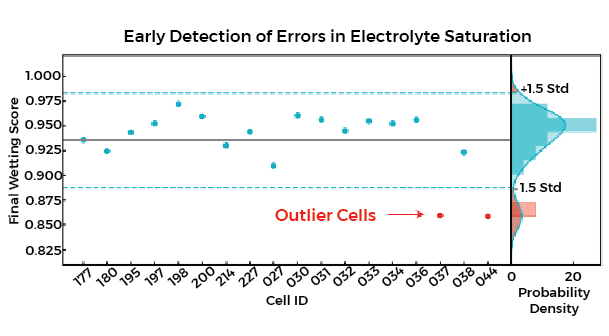
Formation
EchoStat can provide spatially resolved physical information of cells’ uniformity during- and post-formation. This can help cell developers realize the formation process parameters that have the greatest impact on cell performance. With EchoStat’s Cycle Life Prediction model, engineers can understand the intricate relationships between formation protocols and long-term cell performance. This is paramount for iterating towards a formation protocol that minimizes side reactions and optimizes SEI (Solid Electrolyte Interphase) formation, thus preserving capacity and longevity.
Additionally, EchoStat can be used in mass-production for 100% inspection of cells post-formation to provide cycle life prediction (CLP) and assess cell quality with high accuracy. With EchoStat’s CLP model output, cell makers can get access to distribution of cell quality in the batches of manufactured cells, weeks before the end-of-line QC step.
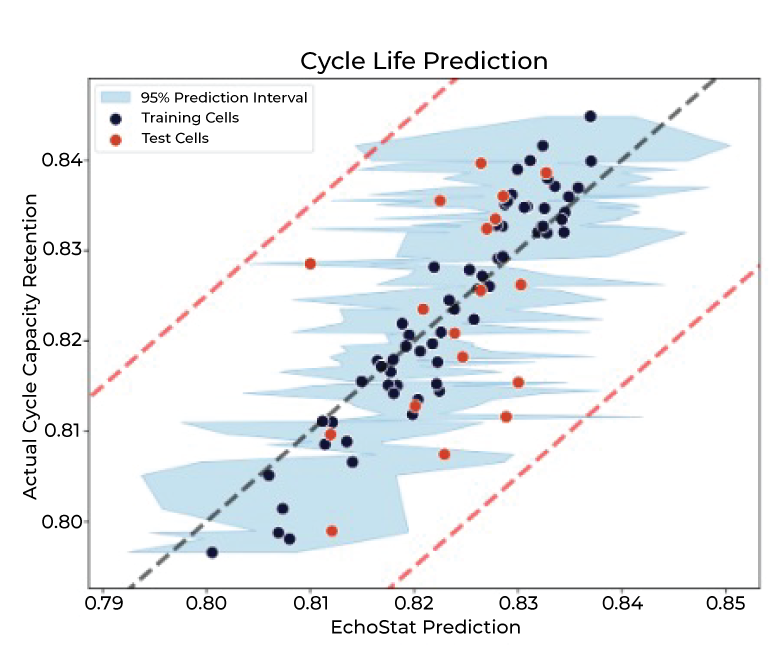
Aging
EchoStat plays a pivotal role between post-formation and pre-aging stages. Utilizing its Defect Detection model, it identifies cells potentially harboring internal defects developed during formation. By inspecting 100% of the cells in every batch, anomalies such as internal shorts or high-resistance weld points—which influence cell uniformity—are flagged. Traditionally, such abnormalities might only be discerned after expensive and lengthy aging cycles. EchoStat’s capability allows engineers to proactively decide which cells should move to the aging process or be subjected to more detailed inspections. This not only optimizes costs and time by preemptively removing flagged cells but also ensures heightened safety, guarding against thermal runaway scenarios and enhancing overall cell longevity.
End-of-line QA/QC
At the End-of-Line (EOL), EchoStat’s NDE technology stands as a cornerstone in ensuring unparalleled cell quality. Scanning every cell in mere seconds, it identifies and flags those containing physical characteristics of manufacturing anomalies or latent defects. This functionality, tied with machine learning algorithms, allows process engineers to draw predictive maintenance insights regarding the machinery involved in the cell production process itself. By monitoring for trends in cell defects, engineers can preemptively address mechanical issues before they lead to costly downtime. Additionally, EchoStat’s dynamic data-driven insights allow for real-time parameter adjustments, fostering a continually optimizing production line dedicated to peak efficiency and product quality. By highlighting critical variances, it ensures every outbound cell aligns with rigorous quality benchmarks, thereby minimizing post-production risks like recalls or safety incidents and preserving brand reputation in a fiercely competitive battery marketplace. This method not only guarantees confidence in batch quality but also provides an invaluable asset for inbound quality checks during battery module or pack assembly.
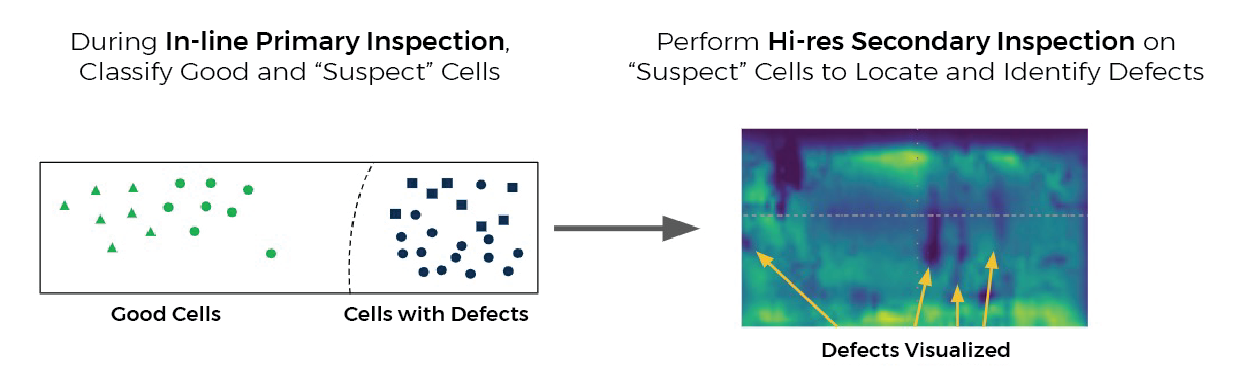
Reimagine Your Production Line with EchoStat
Our CEO and Co-founder, Andrew Hsieh probably summed it up best in an interview for Workweek when he said, “As you generate more primary data up and down the manufacturing ecosystem and feed it into the software layer that sits above the factory, you can build factory-level analytics for factory GMs and executives, offering a more holistic view of their operation.” In short, by providing manufacturers with critical data and insights, EchoStat allows them, in real time, to improve their processes and efficiency–ensuring the production of reliable, safe EV-grade batteries.