A discussion of testing techniques in the manufacturing process, what they’re currently capable of, and how they must improve
The Journal of Power Sources recently published a paper from General Motors R&D, titled: “A review of research needs in nondestructive evaluation for quality verification in electric vehicle lithium-ion battery cell manufacturing.”
The paper outlines the rapid shift from internal combustion engine vehicles to EVs and the battery industry’s resulting need for nondestructive evaluation (NDE) methods and technologies to “drastically evolve to keep pace with this disruptive paradigm shift.”
NDEs are testing methods that take place on the production line, without interrupting the manufacturing process and without causing damage to the part being tested. They must operate on fast timelines, in small spaces, on often-delicate materials. Those constraints present some real challenges, and the overarching theme is that there’s still much more to learn and more progress to be made in NDE testing in EV battery cell manufacturing. While techniques like X-Rays, beta radiation, and infrared show some promise, they also have their limitations and don’t provide sufficient data to be a complete solution at any point in the production process.
Here we’ll distill the findings of the review paper, discuss some of the current testing methods in use in battery cell manufacturing, and highlight a few of the opportunities that exist for the advancement of NDE technology. We’ve also contributed some of our own insights—especially in areas where ultrasound inspection technology and machine learning analytics may apply.
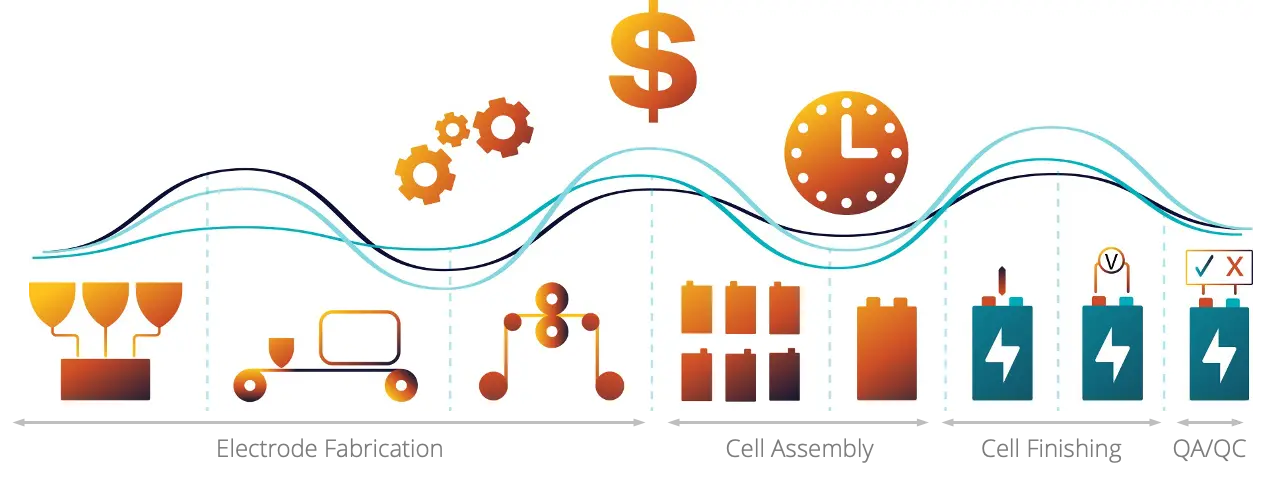
Electrode Manufacturing and Evaluation Methods
1. Electrode Manufacturing
1.1 Slurry mixing
Current best practice
Slurries are suspension liquids that contain the active material to be coated on current collectors to create the anode and cathode of a cell. Slurry quality is determined by its uniformity, stability, and contamination. Inspection at this stage focuses on viscosity and particle distribution or dispersion. Typically, a small portion of the slurry mixture is sampled and measured offline with rheometers, tensiometers, or viscometers. Ultimately, a slurry sample is inherently an audit, and particle agglomeration, foreign debris, contaminants, or inconsistencies in the batch have a high probability of going undetected.
Opportunities
In-situ and sufficiently automated inspection techniques that can measure slurry viscosity, characterize particle dispersion, and detect debris in real-time and without the need for manual sampling of slurry mixtures present the biggest opportunity for NDE testing at this stage of the manufacturing process.
1.2 Coating and drying
Current best practice
The two key influencers here on cell performance are active material loading and dry coating porosity. Both are difficult to measure directly, so it’s common to estimate them. This measurement is done offline by punching a sample, weighing it, measuring its thickness, and estimating based on percentages of slurry constituents. The accuracy relies on assumptions about the slurry quality and weight measurements of solid components in the mixing process. The assumption is mostly dependable, but the technique does require a sample to be removed for measurement. In-line, nondestructive measurements of mass loading and coating consistency exist, including the use of beta radiation, X-rays, and infrared—with varying degrees of accuracy and limitations. For coating adhesion properties, offline peel testing of an electrode sample is the current method of choice.
Opportunities
Opportunities for NDE development should focus on low-cost, in-line processes that increase accuracy, expand property measurement to full-electrode mapping rather than spot-checking, and enable a tighter closed loop of process control. For thickness measurement, adding a wet coating measurement would enable earlier detection of process variation to reduce scrap. For active material loading, a 2D map of the electrode density of dry coatings could verify conformance and catch variations sooner. New methodologies that can directly measure design specifications would also have significant value. Finally, there are currently no technologies to nondestructively inspect coating adhesion and sub-surface issues like cracks, agglomerated particles, or solvent pooling. A method to nondestructively quantify adhesion, delamination, and material distribution issues in-situ or as an audit would greatly benefit the process. This, however, remains a difficult problem to solve.
1.3 Calendering
Current best practice
It’s vital that in-line NDE in the calendering process is able to monitor conformance, especially for porosity. The preferred method is to measure coating thickness and apply known mass-loading estimates. Unfortunately, this technique operates on the assumption that the coating is not compressible—which is not always true. Additionally, in-line vision systems used today can detect surface-level external defects.
Laser micrometers can provide accurate thickness measurements, but only for a very small scan area. Mechanical or digital dial indicators can also measure thickness, but they require surface contact, so they’re generally performed as an audit or when the roll press is stopped. Beta gauges are sometimes used to determine post-calendering coating uniformity of material loading, but suffer from low resolution, noise, and drift over time. The challenge here is that high internal mechanical stresses due to calendering/compaction can damage the roll resulting in delamination, wrinkling, and cracking, which have a huge impact on cell performance and safety.
Opportunities
Considering its high importance, many opportunities exist for NDE of post-calendering coating thickness, porosity, and density. New in-line NDE methods for inspection of sub-surface defects such as mechanical stresses, cracks, particle agglomeration, and delamination are a must-have for the battery industry moving forward. NDE methods used for thin film applications (such as semiconductor, food, and plastic industries) should be considered for electrode inspection and terahertz imaging could be further developed and explored.
1.4 Slitting and notching
Current best practice
Testing for conformance in slitted and notched electrodes consists of dimensional accuracy, coating alignment, and edge quality. These can all be validated by a simple visual inspection.
Opportunities
Most NDE research opportunities in this domain are around debris detection. Since this is the final step of the electrode manufacturing process, there is potential to detect many of the upstream issues at this point.
Quality Assessment Approaches in EV Battery Cell Assembly
2. Cell assembly — folding, stacking and welding
Cell assembly contains many stages where the cell is semi-stationary, such as during welding and pouch lamination. Still, these processes typically last only a few seconds, so any in-line NDE technique must operate accordingly. Otherwise, separate NDE stations have to be established, such that the manufacturing throughput is maintained.
2.1 Folding and stacking
Current best practice
Visual inspection is the predominant mode of NDE for electrode stacking, checking for holes, tears, wrinkles, and alignment issues. An electrical isolation check confirms that the anode and cathode do not have a short circuit. X-Ray computed tomography (CT) has also been used, but this and some other options usually damage the tested cells.
Opportunities
In-line CT would enable electrode stack defect detection and could be placed either directly after stacking or further down the line, since the pouch material is essentially “invisible” to X- ray photons. However, CT speed must increase dramatically to be considered a viable in-line technique. Direct 2D radiography should also be considered, since the faster testing time may make up for the loss of 3D information. A nondestructive technique to detect folded separators in a completed electrode stack would prove very beneficial. Finally, an X-ray could detect large metallic debris, but likely not smaller metallic debris or polymer.
While the implementation of ultrasound remains challenging at this step currently, there is the opportunity to detect anomalies such as electrode misalignment and folding later in the process with ultrasound inspection, once the cell is packaged.
2.1.2 Ultrasonic internal welds
Current best practice
The most common form of inspection for ultrasonic internal welds is destructive testing, where a cell is pulled from the line and mechanically tested for strength. Measured electrical resistance is another metric that can be used to assess weld quality. It’s a delicate balance to obtain measurements that are sensitive enough to detect nonconformities while remaining insensitive to test variations like probe placement.
Opportunities
Ultrasonic welds are especially complex from an NDE perspective because they are multi-layer, thin, and have complicated surface geometry. Techniques don’t necessarily have to be non-contact, however they must be delicate enough to avoid damaging the extremely delicate foils. Finally, inspection must be quick to keep the production line moving.
2.1.3 Laser internal welds
Current best practice
Inspection of laser internal welds presents an even more difficult problem. While thermal propagation serves as an indicator for the laser weld itself, it would not detect lateral foil disconnections. An ultrasonic inspection approach would be limited for several reasons, including the unachievable frequency necessary to detect foil detachment.
Opportunities
X-Ray CT scans, while useful for validation, are lengthy and don’t provide sufficient resolution without damaging the test cell. In-line NDE for multi-layer foil welds isn’t well understood and there are large knowledge gaps to fill—especially for foil detachment detection. The internal weld geometries, accessibility constraints, and defect types pose major challenges. While it would be ideal to develop NDEs capable of detecting foil detachments in fully assembled cells, technology that could accurately inspect a weld while it’s still accessible from both sides would be a great improvement on today’s standard.
2.2. Packaging
Current best practice
This is the process in which the electrode stacks, or jellyrolls, are inserted and sealed into the hard casing, like in prismatic and cylindrical cells or in soft polymer or aluminum bags for pouch cells. One side of the cell—or a fill port in the cell—is not sealed, allowing for the addition of electrolyte in the next process step. Currently, high-potential (hi-pot) testing is the only inspection method used to detect soft shorts between electrodes, separator pinholes, or seal defects.
Opportunities
As most components of the cells are densely packed together in this step, there is a high risk of corner folds, electrode misalignment, electrode stack folding, and tab tearing. Opportunities for NDE testing, like rapid CT and ultrasound, at this step are to detect these minor defects in line for 100% of the cells, which may not be picked up by resistance or hi-pot tests.
Nondestructive Evaluation in Battery Cell Finishing
3.1 Electrolyte Fill and Soak
Current best practice
Weight, viscosity, and surface tension are currently the only measurable metrics during the electrolyte wetting process. But these do not indicate if the electrolyte has fully penetrated and saturated the entirety of the electrode stack. The only way to ensure that is to allow the electrolyte enough time for proper wetting—typically on the order of days.
Opportunities
An NDE technique to estimate or quantify wetting would not only serve as a useful quality check but also provide feedback on initiation of the next process step and result in time savings. The biggest opportunity for adoption would be during the cell and process development phase, i.e. tuning cell designs and process parameters prior to release to high-volume series production of commercial cells.
It should be noted that much progress has been made in the year-plus since the publishing of this review paper, especially in the form of Liminal’s EchoStat technology. EchoStat’s use of ultrasound inspection and machine learning analytics has evolved to quickly and accurately estimate electrolyte wetting quality within the cell. It does so using a dry couplant, without causing any damage to the cell. EchoStat’s electrolyte saturation application enables cell developers to optimize process parameters to be more efficient and effective. In mass manufacturing, EchoStat provides a wetting score for process control and removal of poorly-saturated cells before formation, reducing the cost of scrap.
3.2 Formation
Current best practice
Solid-electrolyte-interphase (SEI) formation is one of the most critical steps in the manufacturing process—it’s also one of the most time- and energy-intensive. Formation protocols are complex recipes involving precise pressure, temperature and charging rate sequences to minimize formation time. There is a need to balance formation time and electrochemical performance of high energy Li-ion batteries. The details are closely guarded by every cell manufacturer since it is the secret ingredient to cell longevity and performance. Current in-line inspection of the formation process involves monitoring the cell’s electrochemical response, e.g. voltage or current over time in comparison to a reference curve.
Opportunities
Most NDE research opportunities in the formation stage must be applicable to a nearly completed cell. Test time is not as much of an issue here though, since the cell is nearly or completely stationary for much of the formation process.
Formation protocol development during R&D and pilot scale can take years. As mentioned above, there are many process parameters that can influence “optimal” SEI quality in cells. Battery experts run extensive multivariate designs of experiments to determine the best formation protocols for their cell chemistries and architectures. However, the true gauge for “best formation protocol” is through long-term cycling performance results, which inherently can take months to years. In-process electrochemical metrics like formation capacity, internal resistance and self-discharge voltage monitoring during aging are not sufficient to assess SEI formation quality. Moreover the impact of formation process parameters like charge and discharge protocol, stack pressure, temperature, etc. on cell performance are not easily measured in-process.
There is a big opportunity in NDE inspection of cell SEI quality with EchoStat, which can provide spatially resolved physical information of cells’ uniformity during and post-formation. EchoStat can help cell developers realize the formation process parameters that have the greatest impact on cell performance, and help iterate significantly faster to determine the “best formation protocol” for manufacturing.
Additionally, EchoStat can be used in mass-production for 100% inspection of cells post-formation to predict cycle life performance (CLP) and assess cell quality with high accuracy. With EchoStat’s CLP model output, cell makers can get access to distribution of cell quality in the batches of manufactured cells, weeks before the end of line QC step. Learn more about how our cycle life prediction is changing quality measurement and control for cell manufacturing in our May blog post.
3.3 Aging
Current best practice
During aging, cells are stored in a temperature-controlled warehouse for periods of two to six weeks, and their open circuit voltage (OCV) is checked periodically without passing current through the battery. If the voltage falls faster than a predetermined rate, i.e. because of an internal defect causing a small “leakage current,” then the cell is rejected. This is often called the “voltage droop” or “self-discharge voltage drop” check.
Opportunities
There is a desire in the industry to reduce aging time, as cells are sitting idle for weeks rather than being shipped to customers. This ties up working capital and also is a source of supply chain risk. There are plenty of opportunities for NDE techniques that are able to more accurately and quickly detect internal defects to reduce aging time. The amount of cell access depends on the plant itself and how they store the cells.
Liminal’s EchoStat can be used in mass-production for inspection after formation and before aging to detect anomalies and internal defects, thus reducing the need for weeks-long aging times. EchoStat can inspect 100% of the cells in each manufactured batch to selectively target anomalous cells for long-term cycling and labor-intensive CT inspection. This approach helps to reduce the overall time and cost associated with cell testing, while also ensuring that only the most critical cells are subjected to more rigorous testing.
End-of-Line Inspection and the Future of Battery Manufacturing
3.4 End of line (EOL) QA/QC
Current best practice
This is the last stage of the cell manufacturing process and the cells are checked to ensure that they conform electrically, structurally and aesthetically. Current EOL testing for quality verification consists of many electrical techniques. Capacitance measurement, internal resistance (ACR, DCR), and open circuit voltage (OCV) are some common electrical tests used to detect defects and predict quality for cell grading. Accessibility at the end of line is naturally a major testing constraint, as most of the components of interest now reside inside the (pouch, prismatic or cylindrical) packaging. That said, this is a crucial testing point; cells at risk of suffering from early failure must be caught before leaving the plant.
At the EOL stage, <0.5% of cells from each manufacturing batch are sampled for 9- to 14-day offline electrochemical tests, CT scans and/or 3- to 6-month cycle testing. The entire batch of cells is usually held in storage while these sample test results are obtained as a proxy for the cell batch quality. However, with this random-sampling approach, defective cells (occurring at parts-per-million (ppm) rates) can slip through without getting tested.
Opportunities
Although the importance of in-line quality verification systems have been discussed at every stage of the manufacturing process, inspection of a fully assembled cell at EOL for redundancy remains crucial. While electrical QC and electrochemical performance testing remain integral to the battery manufacturing industry, there are significant opportunities to enhance EOL QA/QC with new types of inspection methods and data streams. Rapid CT is recognized as one of the promising NDE techniques for this stage. Some experiments have been able to detect particle contamination using short circuit resistance, where internal shorts cause self-discharge, and ultrasound and machine learning has been used to predict the state of charge (SOC) and cycle life performance in cells with advanced signal processing.
EchoStat’s NDE method can inspect 100% of the outbound cells in seconds per scan at the EOL stage, flagging suspicious cells for deeper CT scanning, long term cycling, and other electrochemical QC tests to identify and remove anomalous cells before they leave production. This targeted sampling approach empowers cell manufacturers to have high confidence in their batch quality before cells leave their factories. This application also unlocks value for inbound quality testing for battery module or pack assembly.
Advancing Nondestructive Evaluation for Battery Cell Testing
While an impressive amount of progress has been made in NDE methods, there is still a vast amount of opportunity to apply ultrasonic imaging, machine learning analytics, and other technologies to evolve the battery cell testing process even further. Liminal is committed to providing cell manufacturers with advanced NDE solutions, empowering them to scale up faster and meet the disruptive demand for reliable and cost efficient EV batteries.
Obtain a full copy of the article from ScienceDirect to learn more.